SPM HD
SPM HD® is a patented further development of the Shock Pulse Method (SPM) used for a fast, easy, and reliable diagnosis of the operating condition of rolling element bearings. It provides easy-to-understand condition evaluation in a green-yellow-red scale, as well as crystal-clear spectrums and time signals for further analysis.
Features
-
Fast, easy and reliable diagnosis of bearing condition
-
Easy-to-understand condition evaluation in green-yellow-red scales
-
Identify bearing damages using exceptionally clear spectrums and time signals
-
Monitor applications in a very broad RPM range, including ultra low-speed applications (0.1 - 20 000 RPM range)
Technical description
Advanced digital technique and RPM-based sampling frequency make SPM HD particularly well suited for measurement on low-speed applications. Sophisticated mathematics algorithms make the measuring technique less sensitive to interference from other signals. Extraordinary signal quality and 24 bit A/D conversion provide razor-sharp resolution and exceptional detail in spectrums and time signals. Time signals are very easily interpreted, making the type and extent of the damage simple to determine. SPM HD can be used to monitor applications in the 0.1 - 20 000 RPM range.
Throughout their lifetime, bearings generate shocks in the interface between the loaded rolling element and the raceway. These shocks 'ring' the shock pulse transducer, which outputs electric pulses proportional to the shock magnitude. Unlike vibration transducers, the shock pulse transducer responds at its carefully tuned resonance frequency of about 32 kHz, enabling a calibrated measurement of the shock pulse amplitudes. Shock pulse amplitude is due to three basic factors:
- Rolling velocity (bearing size and rpm)
- Oil film thickness (separation between the metal surfaces in the rolling interface). The oil film depends on lubricant supply as well as alignment and load.
- The mechanical state of the bearing surfaces (roughness, stress, damage, loose metal particles).
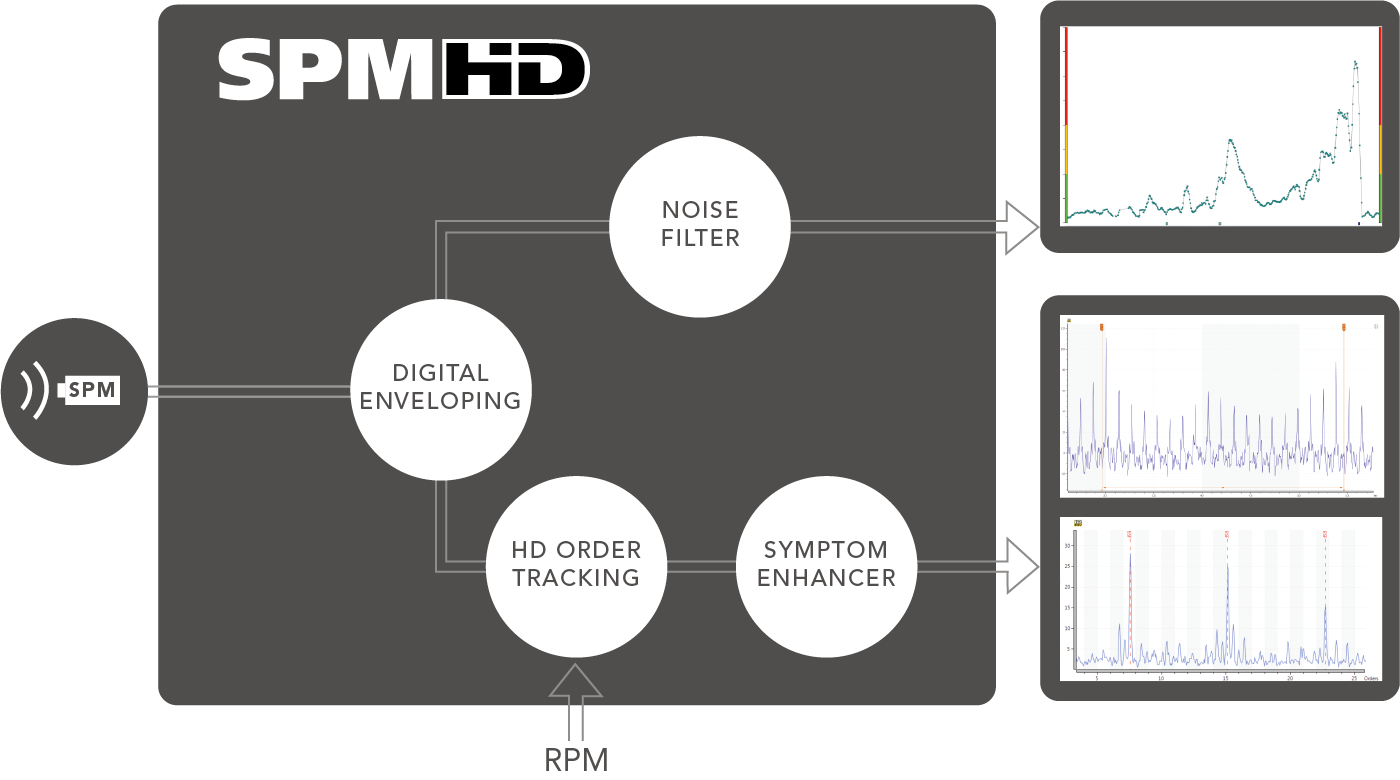
Input data
The effect of rolling velocity on the signal is neutralized by entering rpm and shaft diameter as input data, with 'reasonable accuracy'. This sets an initial value (HDi), the start of the ´normalized' condition scale.
Signal processing
Noise filter: Randomly occurring high readings that may cause false alarms are filtered out by means of the random impact rejection algorithm.
RPM fluctuations are handled with HD Order Tracking, see below.
The Symptom enhancement algorithm looks for repetitive impacts in the time domain. As a result, random signals are suppressed and repetitive signals enhanced.
Output data
- HDm
A scalar value expressed in decibels. It is the primary value to use to determine the severity of the bearing damage. It represents the highest shock pulses found during the measuring cycle. This value is also used for triggering alarms. - HDc
A scalar value expressed in decibels. This value represents the level where 200 shocks/second are present. It is useful to determine the lubrication condition.
- Time signal HD
Extremely useful to locate where in the bearing the potential damage is located. In many cases, it is also possible to determine the nature of the damage (cracked inner race with spalling all around, or a single crack, etc.). The Time signal HD is a result of very advanced digital algorithms where repetitive shocks are enhanced, and random signals are suppressed.
Evaluation
Testing bearings under variable operating conditions have empirically established the initial value and the range of the three condition zones (green-yellow-red). The maximum value places the bearing into the condition zone. The height of the carpet value and delta (HDm minus HDc) indicate lubrication quality or problems with bearing installation and alignment.
HD Order Tracking
On machinery operating under variable speed, analysis with High Definition Order Tracking provides reliable data and crystal clear measuring results even when RPM varies significantly during the course of measurement. More and more machines are speed-controlled, for example, compressors with variable speed drive (VSD) where RPM changes very quickly. Order tracking is applicable in a very wide RPM range, from just a few to thousands of revolutions per minute.
HD Order Tracking is approximately ten times better than traditional order tracking algorithms when RPM is not perfectly stable.
The method uses multiples of rotational speed (orders), rather than absolute frequency (Hz). The purpose of using orders is to lock the display to the rotational speed (1X) and its multiples, meaning that the ordered components in the spectrum always remain in the same position in the display even if the rotational speed varies during measurement.
Two or several spectra from the same machine with variable speed can, therefore, more easily be compared if they are expressed in orders. With order tracking, the frequency range always covers the symptoms of interest, regardless of the rotational speed of the machine.